在对金属进行加工的过程中,零件上时常会出现毛刺。所以,在生产加工过程中,去除各种各样零件的毛刺,需要花费大量的人力、物力。因此,平白浪费了许多成本。那么,如何有效减少金属加工中毛刺的产生呢?下面我们就来从刀具设计方面具体介绍一下。
1、选择合适的刀具材料
刀具材料本身的性能是影响刀具切削性能的主要因素,而刀具在切削的过程中,工作环境很恶劣,刀具既要承受很大的切削力,又要受到高温加热而进行氧化,这样会导致刀具磨损加剧。当刀具磨损后,切削刃会变钝,此时就容易产生粗大的毛刺,这种毛刺十分难以去除。因此,在对刀具进行设计的时候,必须要根据加工要求和工件材料的性能来选择刀具材料。
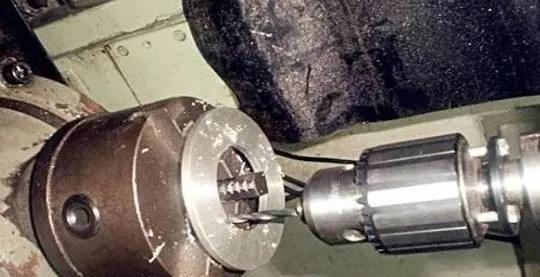
2、选择合理的刀具角度
影响毛刺生成的刀具角度主要有前角、后角、主偏角、副偏角等。如果适当的增大前角,可以有效降低切削的变形,对于减少毛刺生成有一定的帮助。
而适当的增大后角,可以让刃口锋利,减轻刃口对工件材料的挤压,对于减少毛刺的生成也有一定帮助。而主偏角和副偏角主要影响的是残留面积的主要因素,在切削时往往在残留面积上生成毛刺,为了减少毛刺的生成,需要增大主偏角、减少副偏角。
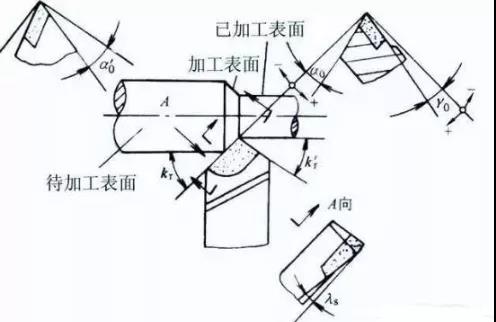
3、采用适宜的刀具结构
根据零件的加工要求以及加工条件,可以采用各种结构形式的刀具来控制毛刺的生成。例如采用复合刀具,在加工过程中,前一刀具切削时生成的毛刺能被后一刀具去除,这样有效控制了毛刺的生成,又能提高加工的质量。在生产中,每种去毛刺方法的加工原理、特点与应用场合都不相同。对于各种零件和加工方法所产生的不同类型的毛刺,采用什么样的去毛刺方法非常重要,影响去毛刺的因素有很多,但是归纳起来主要还是零件加工条件与加工要求,因此,在选择去毛刺的方法上需要考虑到以下问题:1.被加工零件的生产批量、材料特性、结构形状、尺寸大小等因素。2.去毛刺方法的加工能力、经济性、现有去毛刺设备与技术水平。3.去毛刺的副作用。最后通过多次试验,选择确定最佳参数,可以取得良好的效果。